Por qué la comunicación es clave en la transferencia y validación del diseño
- Detalles
- Categoría: Minitab
- Visto: 205
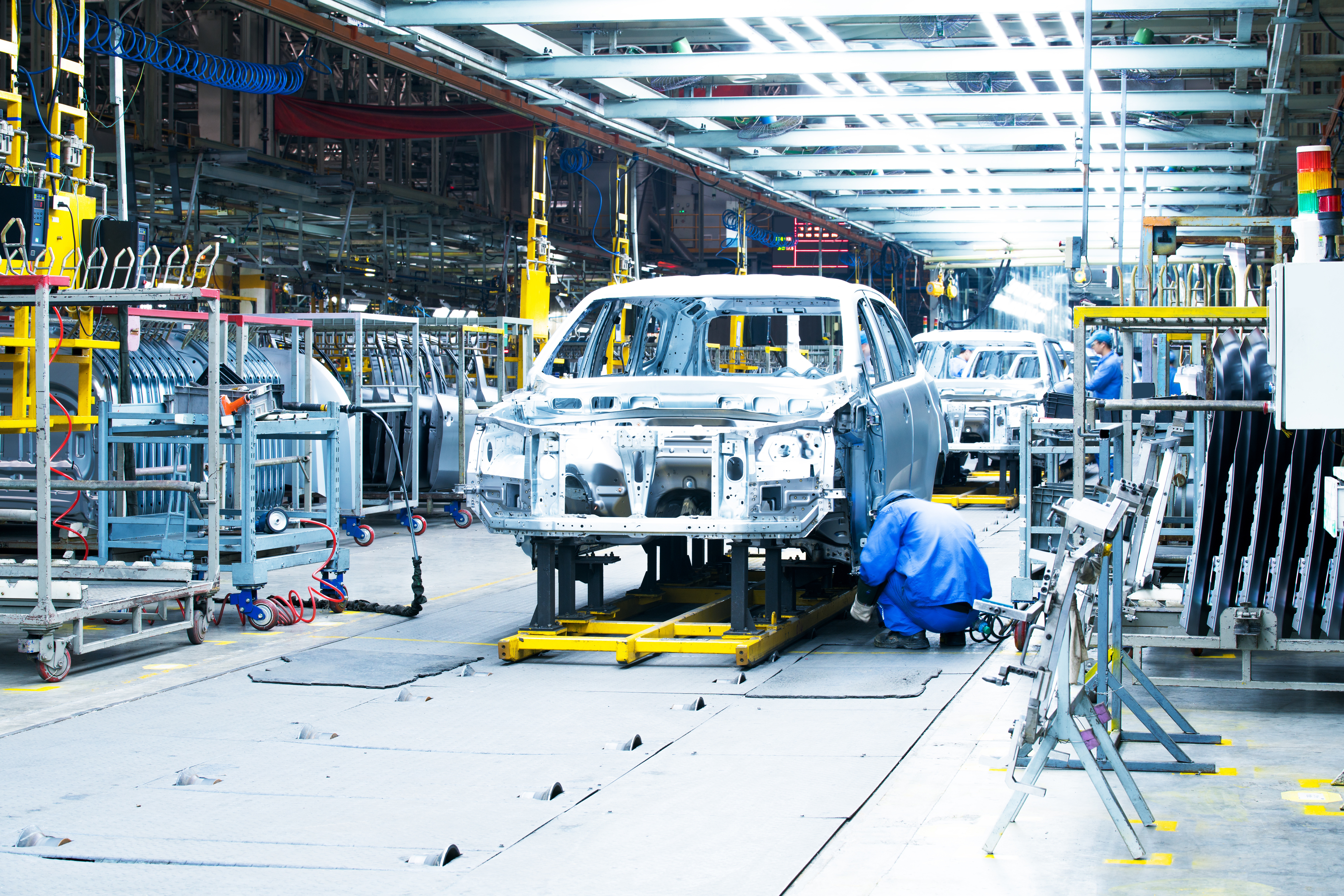
Por Alyssa Sarro.
El proceso de transferencia y validación del diseño es crucial entre la planificación de la investigación y el desarrollo (I+D) y la ejecución del proyecto. Esta etapa garantiza que los diseños se traduzcan con precisión a la producción, minimizando los costosos retrasos y garantizando la calidad del producto. Recientemente, tuve la oportunidad de conversar con Josh Goodman , exingeniero de procesos de uno de los proveedores de primer nivel más importantes del mundo. Su experiencia en este puesto me ha proporcionado valiosos aprendizajes y perspectivas únicas sobre lo que se necesita para tener éxito en un trabajo tan exigente.
Comprensión de la fabricación de piezas de automoción
Antes de profundizar en la conversación, analicemos las complejidades de operar como proveedor de primer nivel en la fabricación de automóviles. Un proveedor de primer nivel en la fabricación de automóviles es una empresa que proporciona piezas o servicios directamente a un fabricante de equipos originales (OEM), como Ford, Toyota o BMW. Nuestro entrevistado supervisó todo el proceso de fabricación, desde las piezas metálicas iniciales hasta el ensamblaje final de los radiadores en una línea semiautomática. Esto combina procesos manuales y automatizados, lo que significa que ciertas tareas son realizadas por máquinas, mientras que otras requieren intervención humana. Su operación funcionaba 24/7 y producía casi 3000 radiadores al día. Estos radiadores se fabrican inicialmente como piezas metálicas, pero luego se sueldan para formar bobinas que permiten que el refrigerante circule por las tuberías y enfríe la transmisión. Este proceso incluye ensamblar un enfriador de aceite en un tanque de plástico, conectar las mangueras y sellar el tanque al radiador metálico. Los tapones de drenaje se instalan manualmente con un taladro; el proceso completo toma un promedio de 30 segundos. Incluso un pequeño cambio en el tiempo de producción puede ahorrar o costar millones, lo que resalta la importancia de la eficiencia. |
|
El problema del diseño
Durante el lanzamiento de un nuevo modelo de coche, un cambio de diseño en el tapón de drenaje planteó un reto importante. El objetivo del cambio era evitar que se utilizaran tapones de drenaje nuevos en modelos antiguos, y viceversa. Este enfoque proactivo buscaba minimizar errores futuros, como el uso de tapones incorrectos. Sin embargo, el equipo de diseño pasó por alto un factor importante: el taladro ya no encajaba automáticamente en los tapones para atornillarlos.
El diseño anterior permitía a los operarios completar el montaje completo del enfriador, las conexiones de las mangueras y la colocación de los tapones de drenaje en aproximadamente 30 segundos antes de pasar la pieza. Este tapón de drenaje de nuevo diseño requería un poco más de intervención humana. Radiador de aluminio de alto rendimiento para coche, económico, OEM B557-15-200DEl taladro debía estar perfectamente alineado con la broca para atornillarlo. Lo que podría no parecer un gran cambio convirtió una operación de 30 segundos en una de 45, lo que representa un aumento del 50 % en el tiempo de producción.
Quizás te preguntes: "¿Y qué? ¿Qué son otros 15 segundos de tiempo de producción?"
Bueno, este aumento en el tiempo de producción tiene muchas implicaciones.
- El proveedor debe aceptar una disminución significativa en las unidades producidas cada día.
- El proveedor tiene que realizar un cambio masivo en el modo en que opera la línea de fabricación para combatir el mayor tiempo de producción.
- El proveedor tiene que contratar más personal para mantener su producción eficiente.
Al final, todos estos ajustes costarían miles o millones de dólares. Josh informó de esto al equipo de diseño, y terminaron retrasando el nuevo diseño del radiador un año entero, lo que obligó al nuevo coche a necesitar el diseño anterior. Así pues, lo que parecía un cambio de diseño menor y proactivo terminó en un grave problema para I+D y la reputación de la empresa.
Cómo evitar los problemas de transferencia de diseño con Minitab Engage
Esta experiencia subrayó la importancia de una validación y revisión exhaustivas durante la etapa de transferencia del diseño. Si los equipos de diseño y fabricación se hubieran comunicado eficazmente, podrían haber anticipado el problema y evitado seguir adelante con el nuevo diseño del tapón de drenaje. Cuando le pregunté a Josh cómo logró evitar este problema en el futuro, comentó que tuvo la suerte de que su siguiente empresa contara con un equipo de diseño en la misma fábrica, actuando como intermediarios entre ambos equipos.
La principal lección de esta experiencia es el papel crucial de la comunicación y la colaboración para prevenir problemas de diseño. No todos los fabricantes pueden permitirse tener un equipo completo de ingeniería de diseño interno para combatir estos problemas, como se observó en esta planta. Entonces, ¿cómo se podría haber evitado esto? Minitab Engage.
Minitab Engage es una plataforma integral diseñada para gestionar, compartir y dar seguimiento a iniciativas de mejora e innovación, desde la generación de ideas hasta su ejecución. Ofrece funciones para la comunicación interfuncional, la colaboración y la coordinación de proyectos, esenciales durante el proceso de transferencia y validación del diseño.
Con Minitab Engage, los equipos de diseño y fabricación podrían haber utilizado su robusto conjunto de funciones para identificar posibles problemas con antelación. Esta lista de funciones incluye:
- CDOV (Concepto, Diseño, Optimización, Verificación): Esta hoja de ruta proporciona un marco claro y detallado para garantizar que todos los aspectos del desarrollo del producto se consideren y aborden exhaustivamente. Permite identificar y mitigar riesgos potenciales en las primeras etapas del proceso, lo que reduce la probabilidad de errores o retrasos costosos y ayuda a garantizar el cumplimiento de todos los requisitos regulatorios.
- Análisis de modos de falla y efectos (FMEA): esta función ayuda a los equipos a anticipar posibles fallas y sus impactos, lo que permite tomar medidas proactivas.
- Matriz de Priorización de Proyectos: Esta matriz proporciona una forma clara y objetiva de evaluar proyectos, garantizando que todos los miembros del equipo comprendan el proceso de toma de decisiones. Al involucrar a todas las partes interesadas en la definición de criterios y la calificación de los proyectos, la herramienta garantiza que todos estén alineados con lo más importante para la organización.
- Mapas de Procesos: Utilice un mapa de procesos para ilustrar el flujo secuencial y la relación entre los pasos de un proceso o procedimiento. Si hubieran mapeado el proceso, podrían haber detectado el paso que falló. Además, sería útil contar con ese mapa de procesos al trabajar con AMEF.
La capacidad de Minitab Engage de facilitar la comunicación y la retroalimentación en tiempo real habría garantizado que ambos equipos estuvieran alineados y preparados para el cambio de diseño del tornillo, lo que habría permitido reducir el trabajo de reelaboración o realizar cambios en la planta de fabricación, evitando en última instancia la demora.
Para concluir mi conversación con Josh, le pregunté cuál, según él, fue la principal lección de su experiencia. Compartió que, para evitar problemas similares en el futuro, es crucial fomentar una comunicación abierta entre los equipos de diseño y fabricación. Fomente la colaboración y las revisiones periódicas para asegurar la alineación antes de llegar al final del proceso. Es mucho más difícil reaccionar cuando un proceso está a punto de finalizar que al principio. Utilizar las funciones y tecnologías de Minitab Engage que facilitan esto lo simplifica.