Caso práctico de usuario: Diseño de un robot de manipulación industrial con MapleSim y Maple
- Detalles
- Categoría: MapleSim
- Visto: 8266
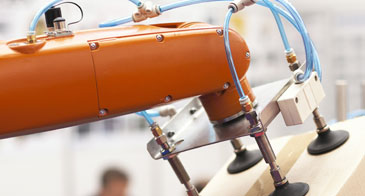
RETO Un proveedor líder de máquinas de envasado experimentaba repetidas fallas en el motor con sus robots manipuladores, que suponen costes sustanciales en el reemplazo de manera regular. SOLUCIÓN La compañía eligió a Maplesoft para desarrollar un modelo parametrizado de alta fidelidad del robot. Usando MapleSim, la compañía simuló la operación del robot y usó Maple para comprender la causa exacta del fracaso con la esperanza de encontrar una solución rentable. RESULTADO Los resultados de MapleSim mostraron a la compañía una solución que desconocían: en lugar de reemplazar los motores en cada robot, podían modificar los perfiles de movimiento del robot para reducir los momentos de mayor par motor. Básicamente, la compañía pudo aplicar una actualización de software a lo que anteriormente se esperaba que fueran costosos reemplazos de hardware en el sitio para motores más grandes. En el futuro, están utilizando sus modelos MapleSim para otros robots, minimizando los altos costes de los componentes diseñados en exceso y las reparaciones inesperadas en el lugar. |
La automatización industrial va en aumento, con máquinas que realizan cada vez tareas más complicadas. Diseñar estas complejas máquinas industriales es un gran desafío. Los ingenieros deben asegurarse de que la máquina que diseñan cumpla con muchos objetivos de rendimiento diferentes para la productividad, el espacio de trabajo, la maniobrabilidad, la carga útil, etc. Al mismo tiempo, también deben desarrollar un diseño que minimice los costes de producción y mantenimiento, como son el uso de motores lo más pequeños posible y los elementos más cortos para los brazos del robot, y la minimización de la carga para reducir el desgaste que lleva a costosas reparaciones, además del tiempo de inactividad. A la luz de tantas complejidades, las organizaciones posiblemente realizarán una ingeniería excesiva de sus productos, invirtiendo en componentes más costosos para reducir fallas imprevistas. Otros intentarán minimizar los costes, pero es más probable que se enfrenten a costosas reparaciones en el lugar cuando se producen fallas inesperadas. El modelado a nivel de sistema ofrece una tercera opción, que proporciona un análisis y visión profunda del rendimiento del producto mucho antes que los prototipos físicos.
Un proveedor líder de máquinas de envasado se acercó al equipo de Soluciones de Ingeniería de Maplesoft para comprender por qué experimentaban fallas recurrentes en los motores en los robots manipuladores desplegados en producción. Se dirigieron a Maplesoft para ayudarles a responder preguntas sobre el diseño de su producto, incluidas muchas preguntas que podrían ser beneficiosas para todos sus futuros diseños de robots:
- ¿Cuál es el tamaño correcto del motor para el robot en todas las condiciones de operación?
- ¿Qué longitud deben tener los elementos para lograr el espacio de trabajo deseado?
- ¿Qué efecto tendrán las diferentes combinaciones de longitudes de elementos en el diseño?
- ¿Cuál es el rendimiento requerido del motor y la caja de cambios en diferentes casos de uso?
El equipo de Soluciones de Ingeniería de Maplesoft aplicó un enfoque de modelado de sistemas paramétricos para responder a estas preguntas. Utilizaron MapleSim para desarrollar un modelo parametrizado de alta fidelidad de los robots manipuladores de la compañía. Luego utilizaron las capacidades de computación avanzadas de Maple para desarrollar herramientas de análisis para examinar el funcionamiento del sistema y su comportamiento dinámico con diferentes conjuntos de valores de parámetros. Estas herramientas de análisis, junto con el modelo de alta fidelidad, proporcionaron a la empresa la información necesaria para determinar cómo prevenir las fallas de sus motores sin ningún hardware adicional nuevo. Pudieron ajustar el perfil de movimiento del robot con el software actualizado, eliminando los momentos en que los motores experimentaban niveles de torsión dañinos. Lo que anteriormente había requerido reemplazos regulares de motores se redujo a una simple actualización de software, ahorrando a la compañía grandes cantidades de dinero en toda su línea de robots. Además de esto, Maplesoft les proporcionó un conjunto de herramientas que podrían configurar fácilmente para su uso en el diseño de productos similares.
Desarrollo de modelos utilizando MapleSim
En la Figura 1 se muestra un ejemplo de un robot típico de manipulación industrial. El modelo de robot está montado en una base de referencia, a la que se conectan tres elementos que forman el brazo del robot. Los elementos son accionados por tres servomotores, que proporcionan el movimiento de rotación y el control con tres grados de libertad. El terminal final consiste en un componente translacional adjunto al tercer elemento, que permite la acción deseada de coger y colocar.
Figura 1: Diseño de un brazo robótico de 3 elementos en MapleSim
Cada una de las estructuras de los elementos incluye componentes de sensores para proporcionar información sobre la fuerza y el par, que luego se puede usar para determinar la fuerza radial, la fuerza axial y los momentos de flexión en cada cojinete. El modelo también incluye sondas integradas en ubicaciones estratégicas dentro del diseño para monitorear las características de rendimiento, como la velocidad y el par motor requeridos, junto con el ángulo y las restricciones de la junta.
Las simulaciones iniciales se corrieron en MapleSim para observar el comportamiento del sistema, con la información de la sonda presentada en varios gráficos. Luego se cargó el modelo en Maple para un análisis en profundidad.
Análisis de diseño utilizando Maple
El equipo de Soluciones de Ingeniería de Maplesoft creó un conjunto de herramientas de análisis en Maple para proporcionar a la empresa una visión profunda de su diseño, asegurando que su producto no estuviera sobredimensionado ni fuera propenso a fallas inesperadas. Aprovechando el modelo totalmente paramétrico de MapleSim y el motor de cálculo simbólico de Maple, las herramientas permitieron a la compañía realizar simulaciones en diversas condiciones operativas para determinar las mejores combinaciones de parámetros de diseño.
La primera herramienta de diseño desarrollada por Maplesoft permitió a la empresa realizar análisis cinemáticos. El análisis cinemático les permitió verificar el espacio de trabajo del robot, visualizar su movimiento y determinar las compensaciones de ruta requeridas. El movimiento del robot se ve afectado por si el codo del robot está configurado para estar en el lado derecho o en el lado izquierdo. Una de las características de la herramienta de análisis cinemático fue realizar los cálculos de cinemática inversa y evaluar las posiciones de ambos codos. Al observar su comportamiento en ambos casos, la compañía pudo tomar una decisión informada sobre en qué lado colocar el codo, una decisión que luego se llevó a cabo y se aplicó a todos los análisis posteriores.
El siguiente paso fue determinar si el robot estaba operando dentro del rango de movimiento permitido y si alguno de los ángulos de la junta excedía el límite deseado.
Figura 2: Análisis de la articulación en Maple.
Para cada articulación había múltiples variables, incluidos el ángulo de la articulación, la velocidad angular y la aceleración angular, y éstas variaban según la trayectoria deseada del movimiento del terminal final. Los resultados mostraron que la trayectoria inicial del diseño del terminal final dio lugar a grandes picos de aceleración angular, lo que indicaba que la empresa necesitaba realizar modificaciones para suavizar el movimiento utilizado para accionar las juntas. El ajuste no solo disminuiría la magnitud de los picos de aceleración, sino que también daría como resultado una menor carga conjunta y una reducción de los requisitos de funcionamiento del motor y del rodamiento. Esta información ayudó a evitar los costos innecesarios de los motores diseñados con exceso.
Si bien la compañía naturalmente quería usar los motores más pequeños posibles, también tenía que asegurarse de que los motores que seleccionaban aún cumplirían con los objetivos de rendimiento del robot. El equipo de Soluciones de Ingeniería de Maplesoft desarrolló una herramienta de análisis para ayudar a la compañía con el dimensionamiento del motor. La velocidad, el par y la energía de los motores se determinaron y graficaron, luego se superpusieron en las curvas de rendimiento del fabricante para los motores seleccionados. Las curvas de rendimiento del motor se seleccionaron de una lista de posibles datos del motor importados a Maple. Para cada uno de los motores, la compañía podría comparar los resultados simulados con datos de diferentes motores de las especificaciones del fabricante. Usando la herramienta de análisis, la compañía pudo considerar diferentes configuraciones de motor capaces de funcionar dentro del rango deseado.
Otra herramienta de análisis desarrollada por Maplesoft fue un barrido paramétrico para observar los efectos de diferentes longitudes de elementos en la operación del robot. La simulación del modelo con diferentes configuraciones de longitud de elementos dentro de un rango permisible predeterminado permitió a la compañía observar los efectos correspondientes en las características de rendimiento, como la velocidad del motor, el par, los requisitos de carga y las variaciones del espacio de trabajo. Maple hace uso automático del procesamiento paralelo, lo que permite que la computadora del usuario ejecute simultáneamente varias simulaciones utilizando diferentes valores de parámetros, y luego presenta los resultados superpuestos en una ventana de visualización para una comparación rápida y fácil.
Figura 3: Ejemplo de resultados de barrido de parámetros para diferentes longitudes de enlace
Al adoptar un enfoque de modelado a nivel de sistema, la compañía pudo mejorar sus procesos de ingeniería, brindándoles una visión profunda del rendimiento de sus productos en una etapa temprana de diseño. La compañía aprovechó este nuevo proceso de diseño para eliminar un importante programa de reemplazo de motores, y continuó realizando mejoras de diseño para futuros ahorros de costos en toda su línea de robots.
Resumen
El equipo de Soluciones de Ingeniería de Maplesoft desarrolló una solución altamente configurable que ayudó a la compañía a enfrentar los desafíos y los costos inesperados que enfrentaron al diseñar robots industriales de manipulación. El desarrollo de un modelo de sistema totalmente paramétrico en MapleSim proporcionó acceso a todos los parámetros del sistema necesarios para analizar y optimizar el comportamiento del sistema. El motor de cálculo simbólico de Maple permitió el desarrollo de una gran cantidad de herramientas de análisis que exploraron las relaciones entre los parámetros del sistema y sus efectos en el rendimiento general. Este nuevo enfoque arrojó luz sobre soluciones que la compañía no sabía que existían, con costos generales tan solo de una pequeña fracción de sus técnicas anteriores para la reparación de motores de robots. Los modelos paramétricos también se están modificando y utilizando en varios diseños de robot de manipulación.
Este caso práctico presenta solo un ejemplo de innovación en los sectores de automatización industrial y maquinaria de envasado. A medida que los requisitos de robots automatizados se vuelven más complejos, esta empresa se dio cuenta del enorme papel que puede desempeñar el modelado a nivel de sistema para impulsar la innovación. Lo que comenzó como el deseo de solucionar un problema simple ha transformado radicalmente su proceso de diseño, acortando los ciclos de diseño y minimizando los costos innecesarios en cada paso del camino.